What is hot dipped galvanized steel?
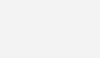
Table of Contents
What is hot-dip galvanized steel?
The manufacturing process of hot-dip galvanized steel goes through many stages.
– Steel washing and chemical treatment to completely remove oxidation stains and dirt on the steel surface.
– Immerse the steel in a pan of molten zinc at 435°C – 455°C (815°F – 850°F).
– The molten zinc reacts with the steel to form an alloy with distinct layers on the surface.
– Ratio :
+ The inner layer is about 25% steel – 75% zinc
+ Outer layer 100% zinc.
– Drain off excess zinc and cool galvanized steel with cold air or water.
– When exposed to air, zinc reacts with O2, H2O, CO2 to form a relatively stable layer of ZnCO3 (Zinc Carbonate).
How is galvanized steel protected?
The resulting Zinc Carbonate layer protects the steel by:
– Creates a layer on the surface between the steel and the air, reducing the possibility of exposure to oxygen.
– The zinc layer acts as an anode, so it slows down the oxidation of steel.
Why use hot-dip galvanized steel?
– Galvanized layer does not peel off like paint coating, creating a stronger protective layer.
– The hot dipping process ensures that the entire steel surface is coated with a uniform zinc coating.
– Customize the thickness of the galvanized layer as required.
– When the zinc surface layer is corroded, the steel plate is still protected due to the function of the galvanized layer acting as an anode.
– Zinc has anti-corrosion properties in high pH environment, so it is often used in industrial zones and coastal areas.
But when exposed to corrosive substances for a long time, the amount of zinc will gradually decrease, in addition, acid rain and salt water also accelerate the corrosion of zinc.
Applications of hot-dip galvanized steel:
Used for steel beams, iron nets, cable tray ladder, railings, roofing sheets, bolts, nuts, steel pipes.
Leave a Reply