How to match 3-phase capacitors
Table of Contents
How to match 3-phase capacitor
There are two main methods of capacitor compensation: static compensation and dynamic compensation, each with different installation and connection methods
- Introduction What is a compensator and capacity compensating capacitor reactive
I. Overview
1./ Static compensation (background compensation):
The compensation arrangement consists of one or more capacitors providing a constant amount of compensation the control can be done by:
- Manual: use CB or LBS ( load – break switch )
- Semi-automatic: use contactor
- Connected directly to the load to energize the compensator circuit at the same time as the load is closed.
+ Advantages: simple and low cost.
+ Disadvantages:
- when load oscillation is likely to lead to overcompensation.
- This is quite dangerous for the system using the transmitter.
- Therefore, this method applies to loads that vary little.
2./ Dynamic compensation (using automatic compensator):
Using auto-compensating condensers, it is possible to variable capacitance capacity to ensure that the power factor reaches the desired value.
+ Advantages: does not cause redundancy and ensures the desired power factor.
+ Disadvantage: higher cost than static compensation.
Therefore, this method is applicable at locations where the active and reactive power varies over a very wide range.
3./ Calculating reactive power and choosing capacitor cabinets:
– Simple Calculation Method: (To choose a capacitor to compensate for a certain load, we need to know the capacity (P) and power factor (Cosφ) of that load):
Assume we have a load capacity P
- The power factor of the load is Cos φ1 → tg φ1 (before compensation)
- The power factor after compensation is Cos 2 → tg φ2.
- The reactive power to be compensated is Qb = P (tgφ1 – tgφ2 ).
From the capacity to be compensated, we choose compensation capacitor accordingly in the catalog table supplier’s capacitor compensation.
II./ Automatic capacitor bank (PFR):
1./ Working principle of automatic compensator :
The automatic capacitor bank consists of the following basic components:
– Controller (PFR)
– The capacitors are connected to the load through the atomat and the contacts of the contactors.
– Current sensor CT
Working principle of PFR:
- The current signal is measured through the CT current transformer and the voltage signal is transferred to the PFR controller.
- Then the microcontroller in the PFR controller calculates the difference between current and voltage, calculates the power factor.
- Due to the numerical method, the power factor can be measured accurate even in the presence of harmonics.
– The controller is designed to optimize reactive power compensation control.
The compensating power is calculated by continuously measuring the reactive power of the system and then compensated by switching the capacitors.
– Controller Important Parameters:
+ Set power factor (Set cosφ): usually in the range of 0.92 – 0.95
+ Sensitivity:
This parameter sets the switching speed.
- High sensitivity the closing speed will be slow and conversely small sensitivity the cutting speed will be fast.
- This sensitivity applies to both the time turning on and off of the capacitor. Sensitivity = 60s/step
+ Repeat closing time:
This is a safety period to prevent closing capacitors of the same level when the capacitor is not fully discharged.
This parameter is usually set larger than the discharge time of the largest capacitor in use.
- Rated level : is the smallest capacitor step used.
- Total distortion due to harmonics :
Overcompensation CSPK: overcompensation of reactive power Q: current will phase faster than voltage
The loading system will be capacitive.
The impedance for the high frequency current component will decrease.
Thus, do increase the influence of the higher order harmonic components.
Fight with the correct scheme:
– Case 1: The phase voltage and current signal supplied to the relay must be in the same phase. (for SK, Mikro, RTR relay type).
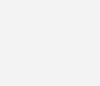
– Case 2: Current signal taken on 1 phase and the voltage signal for the relay is taken on the remaining 2 phases (for SK, Mikro, REGO-Ducati relays).
Particularly for REGO relays, one of three diagrams can be connected: FF-1(Single-phase transformer, remaining 2-phase line voltage); FF2 (Single phase current transformer, phase line voltage with current transformer); FF-n (Variable current and phase voltage in the same phase).
The wiring diagram must be installed in the relay, normally using the FF-1 diagram.
current transformer installation location:
The current transformer that takes the signal to be fed into the capacitor control relay must include both the load current and the capacitor current.
It is recommended to install the correct polarity of the current transformer: current elementary goes in K and goes out L, secondary current signal poles K, L of the current transformer connected to poles K, L of the relay.
(although most relays can automatically select the polarity). Low voltage cabinets with many outputs, current transformers must be installed at the communication cable.
See more:
Leave a Reply