Structure Contactor
-
About contactor:
Start from-contactor is a gas power tool for remote control of switching, reversing and overload protection (if fitted with thermal relays) of three-phase squirrel-cage asynchronous motors.
Magnetic startup has a Contactor called single word starter usually to close disconnect the electric motor. Magnetic starter with two Contactor is a dual magnetic starter used to change the direction of motor rotation called reverse magnetic starter. For short circuit protection, a fuse must be installed.
-
Classification starts from:
Classification of Contactors in electrical cabinets according to the following characteristics:
– According to the transmission principle: we have electromagnetic contactor (electrical transmission by electromagnetic attraction), slightly pressed type, and hydraulic type. Usually in electrical cabinets use electromagnetic contactor.
– In the form of current: DC Contactor and AC Contactor (1-phase and 3-phase Contactor).
Rated voltage of suction coil: 36V, 127V, 220V, 380V, 500V.
– Protective structure against impacts by the surrounding environment: open, protected, against dust, explosive water…
– The ability to change the direction of rotation of the electric motor: Do not reverse the rotation and reverse the rotation.
– Number and type of contacts: Normally open, normally closed.
3. Structure and working principle:
- Construction:
Contactor is composed of components: Electromagnetic mechanism (electromagnet), arc extinguishing system, contact system (main and auxiliary contacts)
a) Electromagnet:
An electromagnet consists of four components:
– Coil used to generate magnet attraction.
– The iron core (or magnetic circuit) of the magnet consists of two parts: the fixed part and the movable cap. The magnet steel core can be of EE, EI or CI form.
– The jet spring has the effect of pushing the movable cover back to its original position
b) Electric arc extinguishing system of control cabinet:
When the contactor in the electrical cabinet switches, an electric arc will appear, causing the contacts to burn and gradually wear out. Therefore, it is necessary to have an arc extinguishing system consisting of many metal partitions placed next to the two contacts, especially at the main contacts of the Contactor in the electrical cabinet.
c) Contactor system in the control cabinet.
The contactor system in the electrical cabinet is in contact with the mobile magnetic core through the mechanical interlocking part. Depending on the carrying capacity of the contacts, we can divide the contactor contacts into two types:
– The main contact of the Contactor in the electrical cabinet: Capable of allowing large currents to pass through (from 10A to several thousand A, for example about 1600A or 2250A). The main contact is the normally open contact that closes when the power is applied to the magnetic circuit of the Contactor in the electrical cabinet, causing the magnetic circuit of the Contactor to absorb again.
– Contactor auxiliary contacts in electrical cabinets: Capable of allowing current to pass through the contacts is less than 5A. The auxiliary contact has two states: Normally closed and normally open of the Contactor in the electrical cabinet.
Normally closed contact is a type of contact in the closed state (with contact between two contacts) when the magnetic coil in the Contactor in the control cabinet is in the resting state (no power supply). This contact opens when the Contactor is in the active state. Otherwise, the contact is normally open.
Thus, the main contact system of the control cabinet is usually installed in the dynamic circuit, while the auxiliary contacts will be installed in the control circuit system of the Contactor in the electrical cabinet (used to control the power supply to the coils magnet wire of the contactor according to the predetermined procedure).
According to some common structure of Contactor in the electrical cabinet, the auxiliary contacts in the electrical cabinet can be linked fixed in number in each set of Contactor, however, there are also some manufacturers that arrange fixed number only. The main contact on each Contactor, while the auxiliary contacts in the electrical cabinet are made into separate separate blocks. When we need to use it, we only add it on the Contactor, the number of auxiliary contacts in this case can be arranged in the electrical cabinet arbitrarily.
Working principle:
1.a) Magnetic starter and two push buttons:
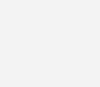
When voltage is supplied to the coil by pressing the start button M, the coil or contactor has a movable steel core and the magnetic circuit is closed: Closes the main contacts to start the motor and closes the normally open auxiliary contact. to maintain the control circuit when letting go of the start button. When the stop button D is pressed, the magnetic starter is cut off, under the action of the compression spring, the moving core returns to its original position; contacts return to the normally open state. Engine stops working. When there is a motor overload, the thermal relay will operate to break the coil circuit, thereby also disconnecting the magnetic start and stop the electric motor.
- b) Reversible magnetic start and three push buttons
When pressing the MT button, the Contactor T coil has a mobile steel core and a closed magnetic circuit; closes the main contacts T to start the motor to rotate in the forward direction and closes the normally open auxiliary contact T to maintain the control circuit when releasing the hand from the push button MT.
To reverse the direction of motor rotation, we press the push button MN to coil Contactor T
electricity, the Contactor N coil has a movable steel core and a closed magnetic circuit; closes the main contacts N, at this time on the motor circuit reverses two wires in three electrical phases causing the motor to reverse and the auxiliary contact is normally open N to maintain the control circuit when letting go of the start button MN motion.
The rotational reversal process is repeated as above.
When the stop button D is pressed, the starter from N (or T) is cut off, the motor stops.
When there is a motor overload problem, the thermal relay will operate to break the coil circuit, thereby also interrupting the magnetic start and stop the electric motor.
Diagram:
a. Rated voltage of Contactor in electrical cabinet
The rated voltage of the Contactor Udm is the voltage of the electrical circuit in the corresponding control cabinet that the main contact must switch on and off, which is the voltage applied to the two ends of the coil of the electromagnet so that the magnetic circuit sucks back.
Rated voltage level in electrical cabinets: 110V, 220V, 440V DC and 127V, 220V, 380V, 500V AC.
b. Rated current of Contactor in electrical cabinet
The rated current of the Contactor in the electrical cabinet Idm is the rated current passing through the main contact in the long-term working mode.
The rated current of the Contactor in the common low-voltage switchboard has the following levels: 10A, 20A, 25A, 40A, 60A, 75A, 100A, 150A, 250A, 300A, 600A. If placed in an electrical cabinet, the rated current must be lower than 10% because of poor cooling, the allowable current through the Contactor must be taken even lower in the long-term working mode.
- Selection and assembly starts from:
Whether a three-phase asynchronous electric motor can work continuously or not depends on the reliability of the magnetic starter. Therefore, verbs must satisfy the following technical requirements:
– Contacts have high wear resistance.
– High closing – cutting capacity.
– Action close – cut definitively.
– Low power consumption.
– Protect the motor from long-term overload (with thermal relay).
Currently in our country, three-phase squirrel-cage rotor asynchronous motors with capacity from 0.6 to 100KW are widely used. To control their operation, we often use magnetic starters. Therefore, in order to facilitate the selection of magnetic starters, manufacturers often not only give the rated amperage but also the capacity of the electric motor, but the magnetic starter serves other voltages together.
In order for boot from to work reliably, when installing it needs to be fastened starting from a vertical plane (allowable inclination from vertical axis 50), grease is not allowed on contacts and moving parts. After installation of the magnetic starter and before operation, check:
– For manual moving parts not to get stuck or entangled.
– The control voltage must match the rated voltage of the coil.
– The contacts must make even and good contact.
– The electrical wiring must be in accordance with the control diagram.
– The thermal relay must be set to start from the wire rod according to the protective fuse.
Leave a Reply